Jak poprawić efektywność energetyczną w polskim przemyśle?
Jak wynika z najnowszego raportu Komisji Europejskiej[1], spośród wszystkich gałęzi rodzimej gospodarki, przemysł wraz rolnictwem zużył w 2015 roku blisko 30% całej energii końcowej w Polsce. To wynik nieco wyższy, niż dziesięć lat wcześniej[2]. W analogicznym okresie w sektorze budownictwa mieszkaniowego i usługowego wskaźnik ten udało się zaś obniżyć – i to o ponad 7%. Jak podkreślają eksperci Paroc, w polskim przemyśle i energetyce wciąż tkwi duże pole do poprawy efektywności energetycznej. Ile może zaoszczędzić pojedynczy zakład produkcyjny, a ile cała gospodarka?
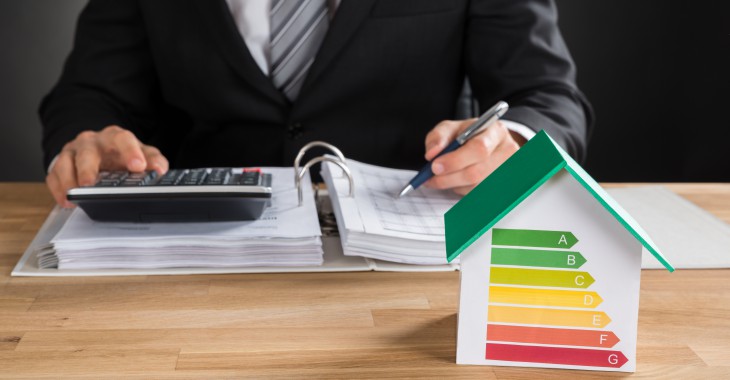
Temat racjonalnego i bardziej zrównoważonego wykorzystania energii powraca w dyskusji publicznej jak bumerang. Najwięcej uwagi od lat poświęca się budownictwu mieszkaniowemu, co jest dosyć logiczne, zważywszy na fakt, iż tradycyjnie jest ono największym konsumentem energii cieplnej i elektrycznej. Znajduje to odzwierciedlenie m.in. w zmieniających się przepisach prawa, które na inwestorów nakładają coraz to większe wymagania względem izolacyjności cieplnej oraz ekologicznych sposobów pozyskiwania energii.
Jak podkreślają eksperci, podobne wysiłki warto przeszczepić na grunt sektora przemysłowego i energetycznego. Podpowiedzi, jak tego dokonać, znaleźć można w doświadczeniach budownictwa. Zdaniem Michała Nękanowicza, Doradcy Technicznego ds. Współpracy z Biurami Projektowymi w Paroc Polska, kadry kierownicze zakładów energetycznych i produkcyjnych powinny skupić się w pierwszej kolejności na maksymalizacji efektywnego okresu eksploatacyjnego oraz na zapobieganiu stratom energii.
O ile w budownictwie udało się zmniejszyć jednostkowe straty ciepła, o tyle w przemyśle wciąż jest sporo do poprawy. Oto prosty przykład: w ciągu ostatnich 20 lat przeciętna grubość izolacji fasad domów wzrosła blisko dwukrotnie. Pozwoliło to zredukować średnie straty ciepła do poziomu poniżej 10 W/m2. W tym samym czasie średnia grubość izolacji w zakładach przemysłowych pozostała praktycznie taka sama, a mówimy tu o stratach ciepła sięgających 150 W/m2.
Ze względu na wysokie temperatury transportowanego medium w instalacjach przemysłowych czy ciepłowniczych, ewentualna utrata ciepła jest znacznie dotkliwsza, niż w przypadku budynków. Ile można zaoszczędzić, modernizując instalację w jednym zakładzie przemysłowym?
Inwestycja, która zwraca się w ciągu miesięcy
Jak wymierny i łatwo dostępny, a relatywnie mało rozpoznany potencjał oszczędności tkwi w termomodernizacji obiektów przemysłowych, obrazują dane raportu TIPCHECK wykonanego dla dużego zakładu przemysłowego w Polsce.
Na miejscu dokonano audytu energetycznego, podczas którego wnikliwie przyjrzano się niezaizolowanym zaworom kołnierzowym instalacji pary wodnej. Za pomocą programów kalkulacyjnych TIPCHECK i PAROC Calculus określono średnie straty ciepła, które wyniosły 1964 W/m. Obliczono także koszty straty ciepła dla pojedynczego zaworu o średnicy DN 250 (2128,24 zł rocznie) oraz DN 350 (7084,89 zł rocznie). Przyjęto, że jeden niezaizolowany zawór odpowiada odcinkowi o długości 1,5 m niezaizolowanego rurociągu o tej samej średnicy.
W celu zwiększenia efektywności energetycznej instalacji, zaproponowano zaizolowanie zaworów kołnierzowych otulinami z wełny kamiennej PAROC Pro Section. I tak, przy zastosowaniu izolacji o grubości jedynie 30 mm w przypadku zaworów DN 250 oraz 60 mm dla zaworów DN 350, udałoby się zmniejszyć jednostkowe roczne zużycie energii o odpowiednio 24.020 kWh oraz 84.271 kWh. Inwestując 248,36 zł (DN 250) lub 386,63 zł (DN 350) w izolację pojedynczego zaworu, można by zaoszczędzić bagatela 1900,86 zł lub 6668,94 zł rocznie. Przedsięwzięcie zwróciłoby się nie w przeciągu lat, lecz miesięcy.
Podejście systemowe – potencjał dla całej Europy
Na to, ile moglibyśmy oszczędzić, warto także spojrzeć przez szerszy pryzmat gospodarki unijnej. Europejska Fundacja Izolacji Przemysłowych (EIIF), organizacja non-profit działająca na rzecz zrównoważonego rozwoju w obrębie sektora energetycznego i produkcyjnego, szacuje potencjał rocznej redukcji energii w 27 krajach członkowskich na poziomie 620.000.000 GJ. Michał Nękanowicz, podsumowuje – tyle moglibyśmy zaoszczędzić, stosując izolacje przemysłowe na opłacalnym, uzasadnionym ekonomicznie poziomie, ograniczając bieżące straty energii z instalacji o 66%.
620.000.000 GJ to tyle, ile rocznie wykorzystuje 15 elektrowni węglowych o mocy 500 MW, 10 milionów gospodarstw domowych lub przemysł Holandii. Taka systemowa inwestycja obniżyłaby konsumpcję energii w tym sektorze o 5% i pozwoliłaby ograniczyć emisję dwutlenku węgla o 49 megaton rocznie. To tyle samo spalin, ile generuje 18 milionów średniej klasy samochodów, przejeżdżających rocznie 12,500 kilometrów. Jak zatem widać, gra jest warta świeczki.
[1] https://ec.europa.eu/energy/sites/ener/files/documents/pocketbook_energy_2017_web.pdf
[2] https://publications.europa.eu/en/publication-detail/-/publication/62b7f2c1-362d-4ea8-a604-dd1eeefe4515/language-en/format-PDF
Komentarze